How Stainless Steel Tanks and Plate Heat Exchangers Work Together?
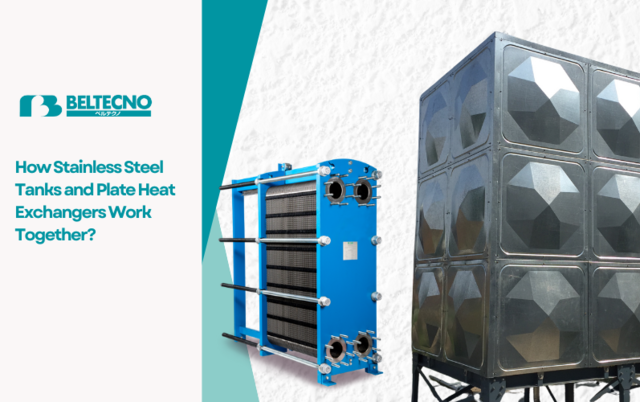
In today's competitive industrial landscape, process optimisation isn't just a goal, it's a necessity.
Companies across sectors are continuously seeking ways to enhance efficiency, maintain product quality, and reduce operational costs.
Two critical components lie at the heart of many industrial processes: stainless steel tanks and plate heat exchangers (PHEs).
While each offers significant standalone benefits, their integration creates a synergistic system that can dramatically improve processing operations.
This blog explores how stainless steel tanks and plate heat exchangers work together to create efficient, reliable, and high-performing industrial systems.
Whether you're in food production, pharmaceuticals, dairy processing, or chemical manufacturing, understanding this powerful combination can help you maximise your operational potential.
Key Benefits of Stainless Steel Storage Tanks
Stainless steel storage tanks have become the gold standard in industrial fluid storage and processing for several compelling reasons:
-
Corrosion Resistance: The chromium content in stainless steel forms a passive oxide layer that resists corrosion from various chemicals, acids, and bases. This makes these tanks ideal for containing aggressive fluids that would quickly damage other materials.
-
Hygiene and Cleanliness: Stainless steel provides a non-porous, smooth surface that prevents bacterial growth and facilitates thorough cleaning. This property is particularly critical in industries with strict sanitary requirements, such as food and pharmaceuticals.
-
Durability and Longevity: With proper maintenance, stainless steel tanks can remain in service for decades. Their structural integrity holds up under diverse operating conditions, from extreme temperatures to high pressure.
-
Low Maintenance: The inherent properties of stainless steel reduce the need for frequent replacements or repairs, decreasing downtime and maintenance costs over the equipment's lifetime.
-
Customisation Options: Manufacturers can easily customise stainless steel tanks with various finishes, ports, agitators, and accessories to meet specific process requirements.
Read: Facts about Stainless Steel Water Tanks
Common Applications of Stainless Steel Storage Tanks
Stainless steel storage tanks serve as workhorses across numerous industries:
-
Water Treatment: For storage, mixing, and chemical dosing.
-
Food Processing: For cooking, mixing, and storage of ingredients and final products.
-
Pharmaceutical Manufacturing: For the preparation and storage of sensitive compounds.
-
Dairy Industry: For pasteurisation and storage of milk and dairy products.
What Are Plate Heat Exchangers?
How They Work
Plate heat exchangers represent one of the most efficient designs for thermal transfer between fluids. They consist of multiple thin, corrugated plates assembled to create alternating channels:
-
The plates are designed with gaskets, brazing, or welding to seal and separate the fluid channels
-
Hot and cold fluids flow through alternate channels in counter-current directions.
-
The corrugated design creates turbulence that enhances heat transfer, while the thin plate material allows rapid thermal conduction.
Advantages of Plate Heat Exchangers
The unique design of PHEs offers several advantages over traditional shell-and-tube heat exchangers:
-
High Heat Transfer Efficiency: The turbulent flow and large surface area achieve 3-5 times higher heat transfer coefficients than shell-and-tube designs.
-
Compact Design: PHEs require significantly less floor space, up to 80% less than traditional heat exchangers with equivalent capacity.
-
Easy Maintenance: The plate pack can be disassembled for cleaning, inspection, and replacement of individual plates or gaskets.
-
Scalability: Capacity can be easily adjusted by adding or removing plates, allowing systems to grow with production needs.
-
Precision in Temperature Control: The counter-current flow and high efficiency enable precise temperature control, often within 1°C of target values.
Typical Uses of Plate Heat Exchangers
PHEs excel in applications requiring efficient heat transfer:
-
Pasteurisation: Precise heating and cooling of dairy products, beverages, and liquid foods
-
Chemical Heating/Cooling: Temperature control in chemical reactions and processes
-
Pharmaceutical Temperature Regulation: Maintaining exact temperatures for drug manufacturing
-
HVAC Systems: Energy-efficient heat recovery and transfer in buildings
How They Work Together: A Synergistic System
The integration of stainless steel tanks and plate heat exchangers creates a processing system greater than the sum of its parts.
1. Temperature Control for Stored Fluids
When connected to stainless steel tanks, PHEs can rapidly adjust and maintain the temperature of stored fluids:
-
Products can be quickly heated or cooled without transferring between containers
-
Batch processing becomes more efficient with reduced heating/cooling times
-
Temperature ramp rates can be precisely controlled for sensitive processes
2. Continuous Recirculation and Temperature Uniformity
One of the greatest challenges in large tanks is maintaining uniform temperature throughout the fluid volume:
-
PHEs can continuously recirculate tank contents to prevent temperature stratification
-
This ensures consistent processing conditions for the entire batch
Uniform temperatures lead to consistent product quality and predictable process times
3. Energy Efficiency and Heat Recovery
The combination creates opportunities for significant energy savings:
-
Heat from one process can be transferred to another via PHEs
-
Cooling energy can be recovered and reused
Waste heat from finished products can preheat incoming raw materials
4. Facilitating CIP (Clean-in-Place) Systems
Maintaining hygienic conditions is simplified:
-
CIP solutions can be heated to optimal cleaning temperatures via PHEs
-
The same PHEs used for processing can often serve dual purposes in cleaning cycles
-
This eliminates the need for system disassembly, reducing downtime and labour costs
Design Considerations for Integration
Successful integration requires attention to several key factors:
-
Material Compatibility: Using the right grade of stainless steel (often 316L for corrosive environments) for both tanks and PHE plates ensures longevity and prevents contamination.
-
Pumping and Flow Requirements: Properly sized pumps and piping ensure optimal flow rates through the PHE while minimizing energy consumption.
-
Insulated Piping and Valve Systems: Thermal efficiency is preserved through proper insulation of all connection points between tanks and exchangers.
-
Automation and Sensors: Temperature probes, flow meters, and control systems enable precise process management and documentation.
-
Cleaning Protocols and Access: Designing systems with CIP capabilities from the outset simplifies maintenance and ensures hygienic operation.
Benefits of Integration
Organizations implementing integrated stainless steel tank and PHE systems show significant operational improvements:
-
Higher Efficiency and Shorter Production Cycles: Process times can be reduced by up to 50% through rapid, uniform heating and cooling.
-
Consistent Product Quality: Temperature uniformity leads to predictable, repeatable results batch after batch.
-
Reduced Energy Costs: Heat recovery and efficient transfer can reduce energy consumption significantly compared to conventional systems.
-
Reliability and Lower Maintenance: The durability of stainless steel combined with the serviceability of PHEs reduces downtime and maintenance costs.
-
Easier Regulatory Compliance: The hygienic properties and documentation capabilities simplify compliance with FDA, USDA, and other regulatory requirements.
Why Choose Beltecno SS Tanks for Your Industry?
Beltecno is a trusted name in the SS tank manufacturing industry, with advanced manufacturing facilities and Japanese technology at its core.
We are the experts in delivering tailored stainless steel storage tanks for diverse industrial and commercial applications.
Our Highlights:
-
Our tanks are made from 304/316-grade stainless steel, which makes them corrosion-resistant and hygienic.
-
We deliver tank capacity ranges from 500L to 100,000L+. So, whether you are looking for a small or huge capacity storage tank, we have tailor-made solutions for you.
-
Our tanks are pressure-tested, leak-proof designs, and welded using advanced Japanese technology. So, you don’t have to worry about frequent maintenance costs.
-
We understand the value of your money, so we have engineering consultation and post-sales service to solve any queries from ordering to post-delivery.
-
Beltecno is available for global delivery, and no, our delivery process doesn’t change; it’s always fast and efficient, no matter where you are.
-
All products comply with manufacturing standards. We ensure that the solutions meet essential regulatory requirements across global markets, especially for industries like food, pharma, and chemicals.
Conclusion
The integration of stainless steel tanks and plate heat exchangers represents a powerful approach to industrial process optimization.
Whether you're designing a new processing facility or looking to upgrade existing equipment, considering this synergistic combination could provide significant competitive advantages.
Need help choosing the right tank? Get in touch with Beltecno’s experts today. Contact Us!